Compoziția chimică a nisipului ceramic este în principal Al2O3 și SiO2, iar faza minerală a nisipului ceramic este în principal faza de corindon și faza de mulit, precum și o cantitate mică de fază amorfă.Refractaritatea nisipului ceramic este, în general, mai mare de 1800°C și este un material refractar din aluminiu-siliciu de înaltă duritate.
Caracteristicile nisipului ceramic
● Refractaritate ridicată;
● Coeficient mic de dilatare termică;
● Conductivitate termică ridicată;
● Forma sferică aproximativă, factor de unghi mic, fluiditate bună și capacitate compactă;
● Suprafata neteda, fara fisuri, fara denivelari;
● Material neutru, potrivit pentru diverse materiale metalice de turnare;
● Particulele au rezistență mare și nu se sparg ușor;
● Gama de dimensiuni ale particulelor este larg, iar amestecarea poate fi personalizată în funcție de cerințele procesului.
Aplicarea nisipului ceramic în piese turnate pentru motoare
1. Utilizați nisip ceramic pentru a rezolva nervurile, lipirea nisipului, miezul spart și deformarea miezului de nisip a chiulasei din fontă
● Blocul cilindrilor și chiulasa sunt cele mai importante piese turnate ale motorului
● Forma cavității interioare este complexă, iar cerințele pentru acuratețea dimensională și curățenia cavității interioare sunt ridicate
● Lot mare

Pentru a asigura eficiența producției și calitatea produsului,
● Producția de linie de asamblare cu nisip verde (în principal linie de coafare hidrostatică) este utilizată în general.
● Miezurile de nisip folosesc, în general, procesul de cutie rece și nisip acoperit cu rășină (miez de coajă), iar unele miezuri de nisip folosesc procesul de cutie fierbinte.
● Datorită formei complexe a miezului de nisip al blocului cilindric și al turnării capului, unele miezuri de nisip au o zonă de secțiune transversală mică, partea cea mai subțire a unor blocuri cilindrice și a miezurilor cămașei de apă ale chiulasei este de numai 3-3,5 mm și ieșirea de nisip este îngustă, miezul de nisip după turnare înconjurat de fier topit la temperatură înaltă pentru o lungă perioadă de timp, este dificil să curățați nisipul și este nevoie de echipamente speciale de curățare etc. În trecut, tot nisipul de siliciu era folosit la turnare producție, care a cauzat probleme de lipire a venelor și a nisipului în piesele turnate ale cămășii de apă ale blocului cilindric și chiulasei.Deformarea miezului și problemele miezului spart sunt foarte frecvente și greu de rezolvat.
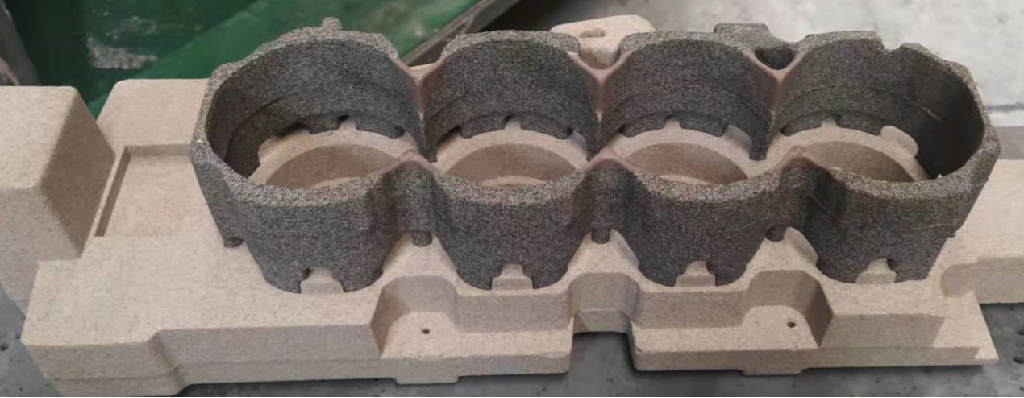
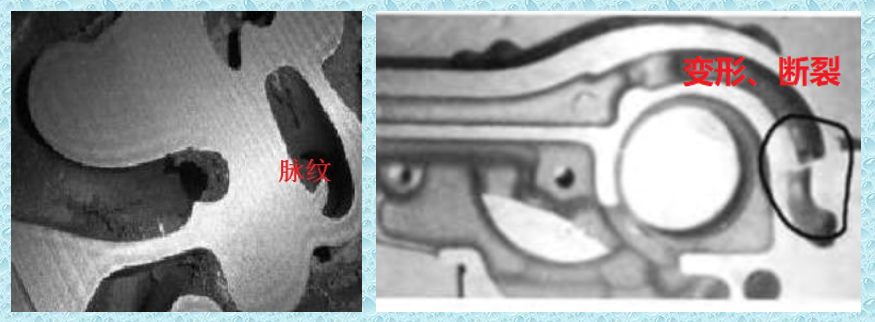
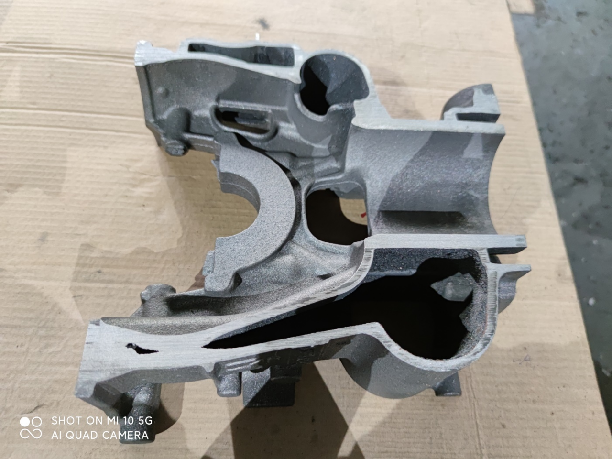
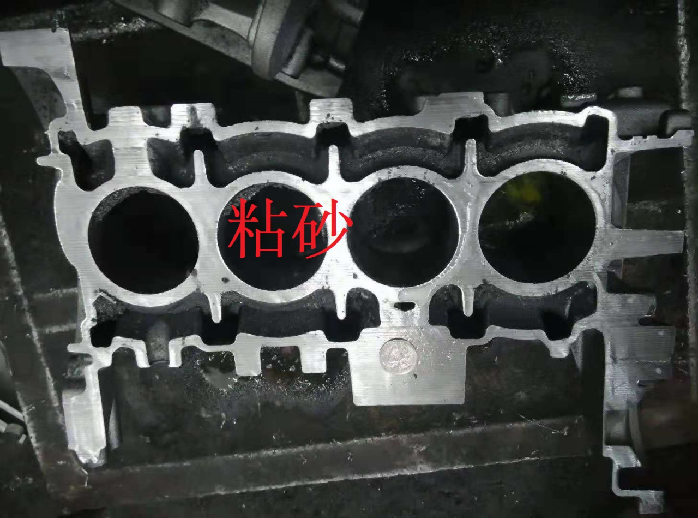
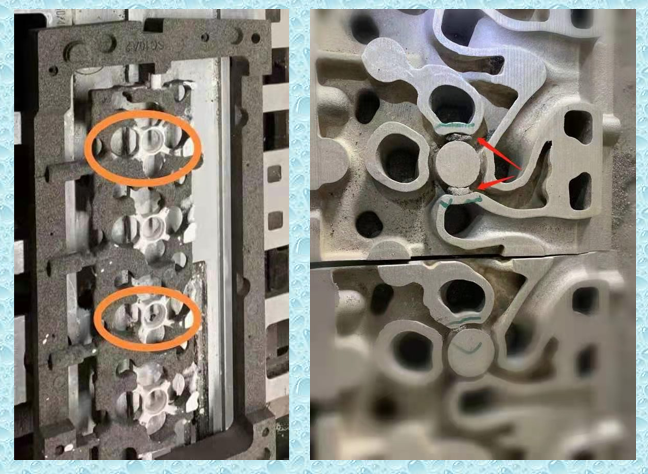
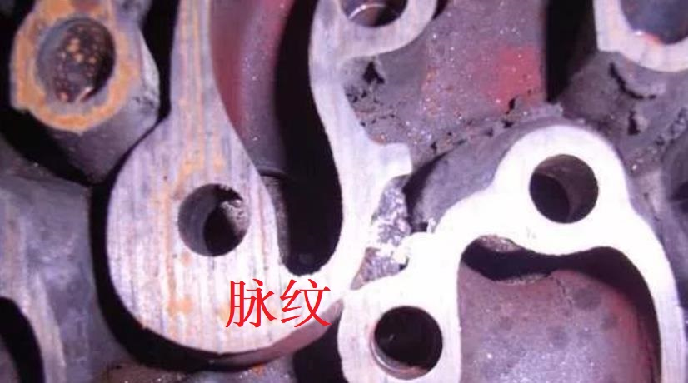
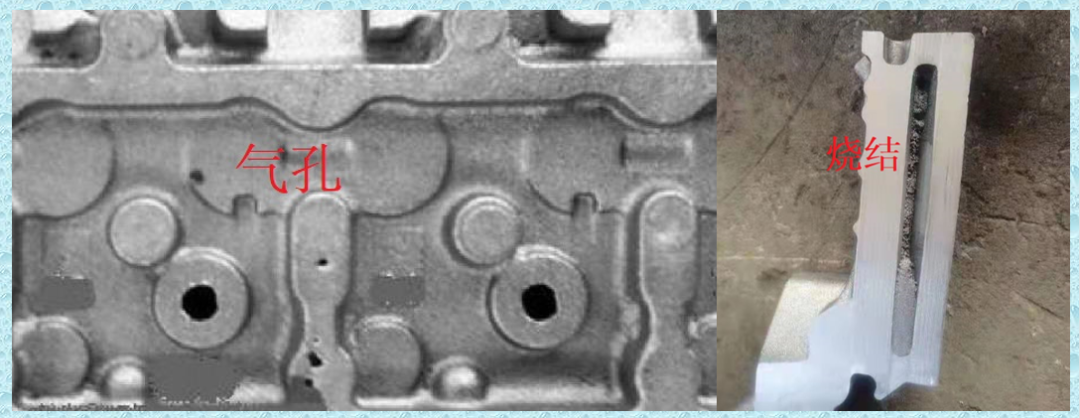
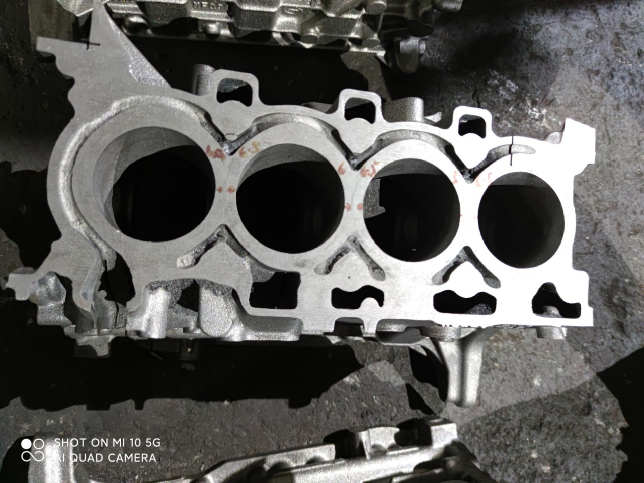
Pentru a rezolva astfel de probleme, începând cu anul 2010, unele companii autohtone de turnare a motoarelor bine-cunoscute, cum ar fi FAW, Weichai, Shangchai, Shanxi Xinke etc., au început să cerceteze și să testeze aplicarea nisipului ceramic pentru a produce blocuri de cilindri, mantale de apă ale chiulasei și canale de ulei.Miezurile egale de nisip elimină sau reduc efectiv defectele, cum ar fi sinterizarea cavității interioare, lipirea nisipului, deformarea miezului de nisip și miezurile sparte.
Următoarele imagini sunt realizate cu nisip ceramic cu proces de cutie rece.
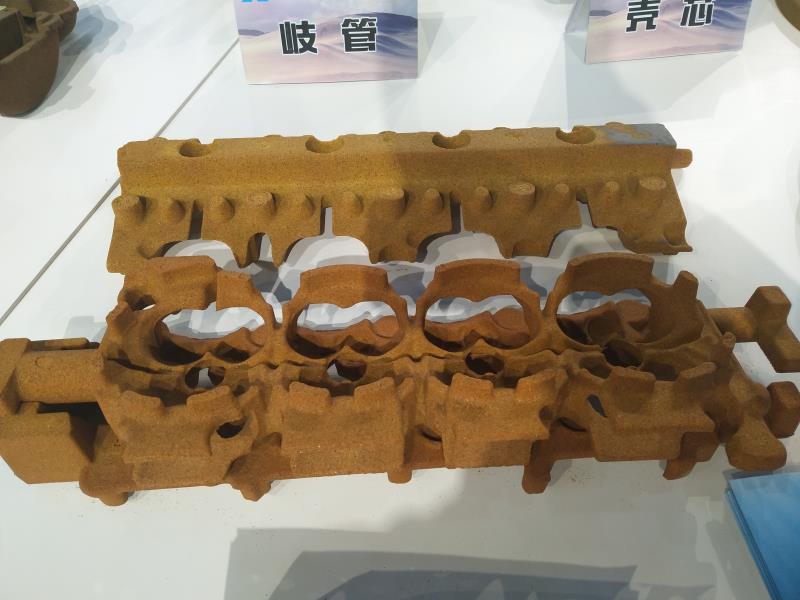
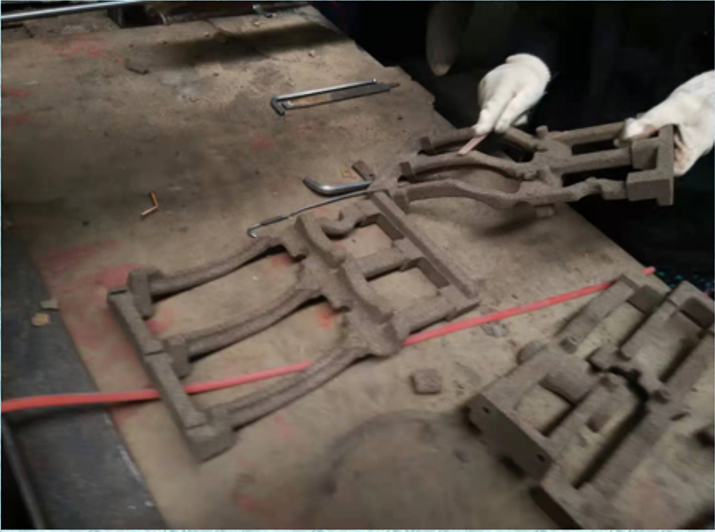
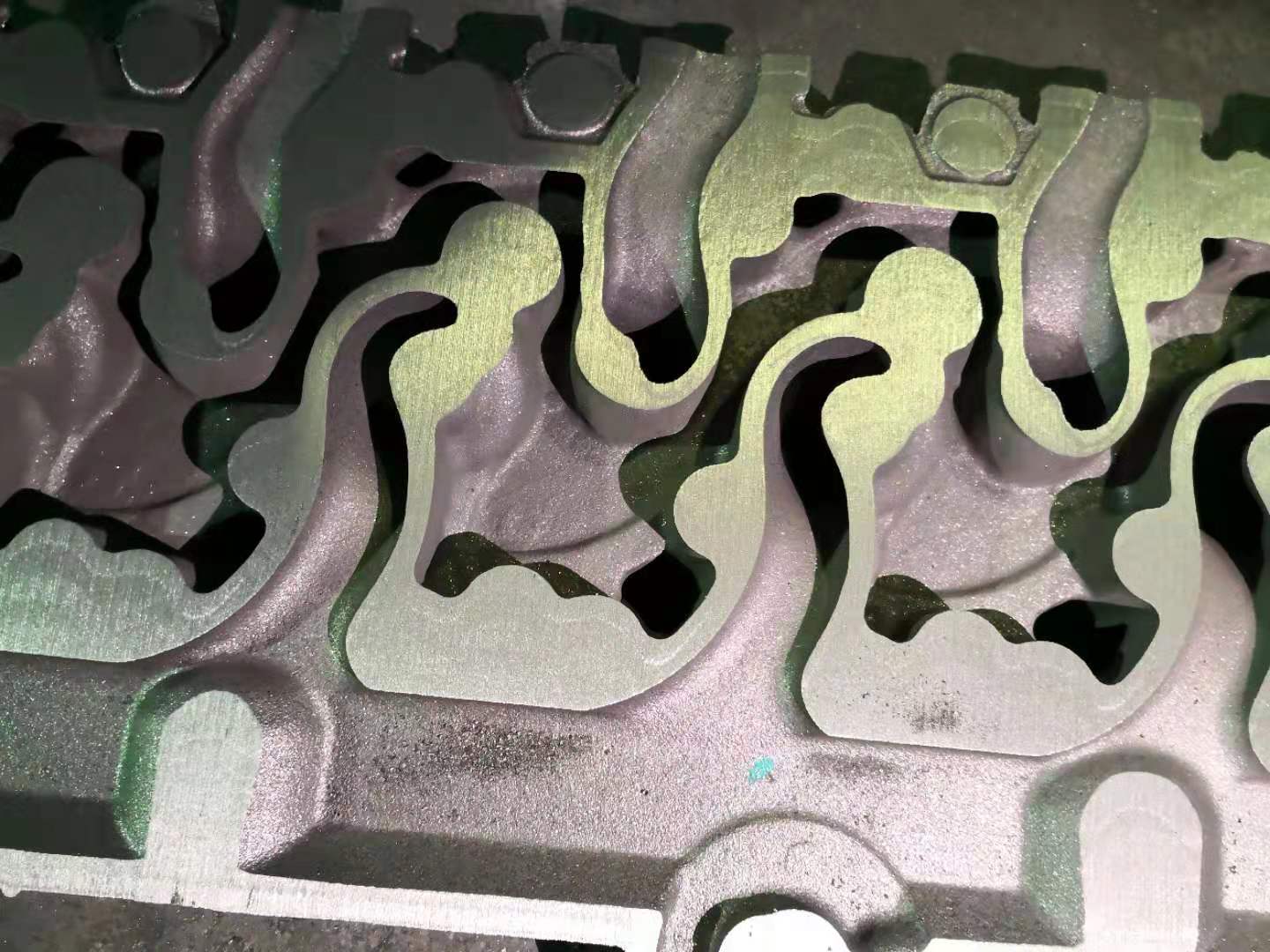
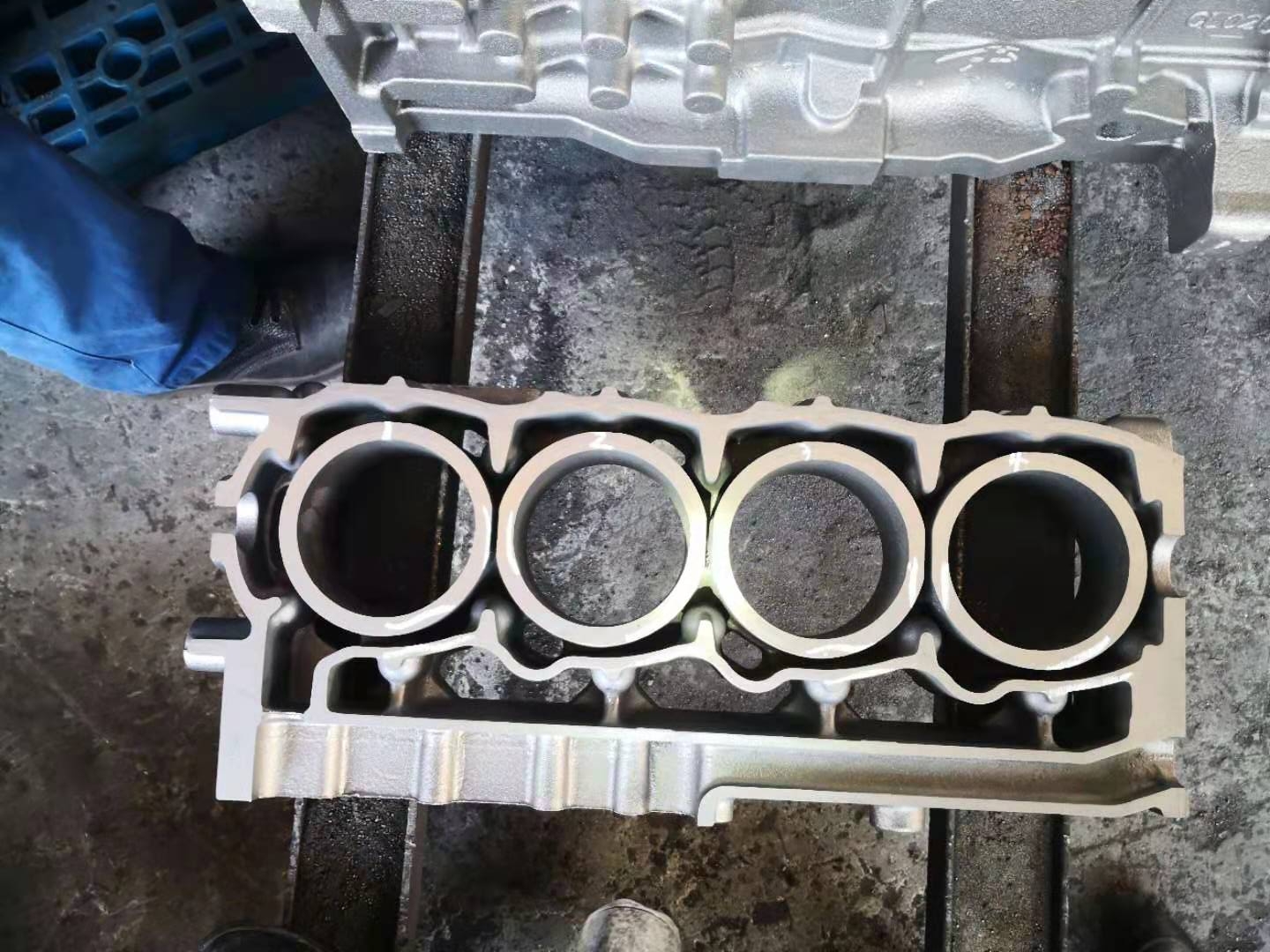
De atunci, nisipul ceramic mixt de spălare a fost promovat treptat în procesele cutie rece și cutie fierbinte și aplicat pe miezurile mantalei de apă a chiulasei.Este în producție stabilă de mai bine de 6 ani.Utilizarea curentă a miezului de nisip cutie rece este: în funcție de forma și dimensiunea miezului de nisip, cantitatea de nisip ceramic adăugată este de 30%-50%, cantitatea totală de rășină adăugată este de 1,2%-1,8% și rezistența la tracțiune este de 2,2-2,7 MPa.(Date de testare a probelor de laborator)
rezumat
Blocul cilindrului și piesele din fontă a capului conțin multe structuri înguste cu cavități interioare, iar temperatura de turnare este în general între 1440-1500°C.Partea cu pereți subțiri a miezului de nisip este ușor sinterizat sub acțiunea fierului topit la temperatură înaltă, cum ar fi fierul topit care se infiltrează în miezul de nisip, sau produce o reacție de interfață pentru a forma nisip lipicios.Refractaritatea nisipului ceramic este mai mare de 1800 ° C, între timp, densitatea reală a nisipului ceramic este relativ mare, energia cinetică a particulelor de nisip cu același diametru și viteză este de 1,28 ori mai mare decât cea a particulelor de nisip siliciu la împușcarea nisipului, ceea ce poate crește densitatea miezurilor de nisip.
Aceste avantaje sunt motivele pentru care utilizarea nisipului ceramic poate rezolva problema lipirii nisipului în cavitatea interioară a pieselor turnate de chiulasă.
Mantaua de apă, părțile de admisie și evacuare ale blocului cilindrilor și ale chiulasei au adesea defecte cu nervuri.Un număr mare de cercetări și practici de turnare au arătat că cauza principală a defectelor de nervuri de pe suprafața de turnare este expansiunea prin schimbare de fază a nisipului de siliciu, care provoacă stres termic duce la fisuri pe suprafața miezului de nisip, ceea ce provoacă fierul topit. pentru a pătrunde în crăpături, tendința venelor este mai mare mai ales în procesul cutie rece.De fapt, rata de dilatare termică a nisipului de siliciu este de până la 1,5%, în timp ce rata de dilatare termică a nisipului ceramic este de numai 0,13% (încălzit la 1000°C timp de 10 minute).Posibilitatea de fisurare este foarte mica acolo unde pe suprafata miezului de nisip datorita tensiunii de dilatare termica.Utilizarea nisipului ceramic în miezul de nisip al blocului cilindric și al chiulasei este în prezent o soluție simplă și eficientă la problema nervurilor.
Miezurile de nisip complicate, cu pereți subțiri, lungi și înguste ale chiulasei cu manta de apă și miezurile de nisip ale canalului de ulei al cilindrului necesită rezistență ridicată (inclusiv rezistență la temperaturi ridicate) și duritate și, în același timp, trebuie să controleze generarea de gaz a nisipului de miez.În mod tradițional, procesul de nisip acoperit este utilizat în cea mai mare parte.Utilizarea nisipului ceramic reduce cantitatea de rășină și obține efectul de rezistență ridicată și generare scăzută de gaz.Datorită îmbunătățirii continue a performanței rășinii și a nisipului brut, procesul de cutie rece a înlocuit din ce în ce mai mult o parte a procesului de nisip acoperit în ultimii ani, îmbunătățind considerabil eficiența producției și îmbunătățind mediul de producție.
2. Aplicarea nisipului ceramic pentru a rezolva problema deformării miezului de nisip a țevii de evacuare
Colectivele de evacuare funcționează în condiții alternate de temperatură ridicată pentru o lungă perioadă de timp, iar rezistența la oxidare a materialelor la temperaturi ridicate afectează direct durata de viață a galeriilor de evacuare.În ultimii ani, țara a îmbunătățit continuu standardele de emisie ale eșapamentului auto, iar aplicarea tehnologiei catalitice și a tehnologiei de turboalimentare a crescut semnificativ temperatura de lucru a galeriei de evacuare, atingând peste 750 °C.Odată cu îmbunătățirea în continuare a performanței motorului, temperatura de lucru a galeriei de evacuare va crește, de asemenea.În prezent, se utilizează în general oțel turnat rezistent la căldură, cum ar fi ZG 40Cr22Ni10Si2 (JB/T 13044), etc., cu o temperatură rezistentă la căldură de 950°C-1100°C.
Cavitatea interioară a galeriei de evacuare este, în general, necesară să fie lipsită de fisuri, închideri la rece, cavități de contracție, incluziuni de zgură etc. care afectează performanța, iar rugozitatea cavității interioare trebuie să nu fie mai mare decât Ra25.În același timp, există reglementări stricte și clare cu privire la abaterea grosimii peretelui țevii.Pentru o lungă perioadă de timp, problema grosimii neuniforme a peretelui și a abaterii excesive a peretelui conductei galeriei de evacuare a afectat multe turnătorii ale galeriei de evacuare.

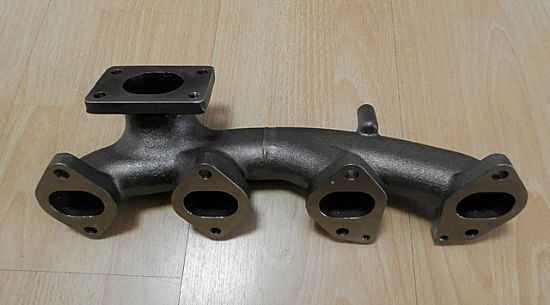
O turnătorie a folosit pentru prima dată miezuri de nisip acoperite cu nisip de silice pentru a produce colectoare de evacuare din oțel rezistente la căldură.Datorită temperaturii ridicate de turnare (1470-1550°C), miezurile de nisip s-au deformat ușor, rezultând fenomene de depășire a toleranței în grosimea peretelui conductei.Deși nisipul de silice a fost tratat cu schimbare de fază la temperatură înaltă, datorită influenței diferiților factori, încă nu poate depăși deformarea miezului de nisip la temperatură ridicată, rezultând o gamă largă de fluctuații ale grosimii peretelui conductei. , iar în cazurile severe, va fi casat.Pentru a îmbunătăți rezistența miezului de nisip și a controla generarea de gaz a miezului de nisip, s-a decis să se utilizeze nisip acoperit cu nisip ceramic.Când cantitatea de rășină adăugată a fost cu 36% mai mică decât cea a nisipului acoperit cu nisip de siliciu, rezistența la încovoiere la temperatura camerei și rezistența la încovoiere termică au crescut cu 51%, 67%, iar cantitatea de generare de gaz este redusă cu 20%, ceea ce îndeplinește cerințe de proces de rezistență ridicată și generare scăzută de gaz.
Fabrica folosește miezuri de nisip acoperite cu nisip de siliciu și miezuri de nisip acoperite cu nisip ceramic pentru turnarea simultană, după curățarea pieselor turnate, acestea efectuează inspecții anatomice.
Dacă miezul este făcut din nisip acoperit cu nisip de siliciu, piesele turnate au o grosime neuniformă a peretelui și un perete subțire, iar grosimea peretelui este de 3,0-6,2 mm;când miezul este realizat din nisip acoperit cu nisip ceramic, grosimea peretelui turnării este uniformă, iar grosimea peretelui este de 4,4-4,6 mm.după cum urmează imaginea
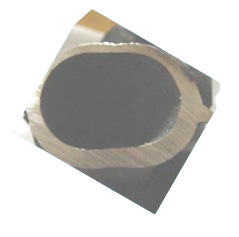
Nisip acoperit cu nisip de siliciu
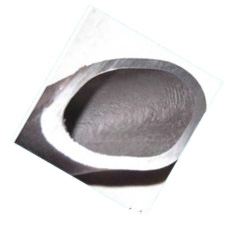
Nisip acoperit cu nisip ceramic
Nisipul acoperit cu nisip ceramic este folosit pentru a face miezuri, ceea ce elimină ruperea miezului de nisip, reduce deformarea miezului de nisip, îmbunătățește considerabil precizia dimensională a canalului de curgere al cavității interioare a galeriei de evacuare și reduce lipirea nisipului în cavitatea interioară, îmbunătățind calitatea piese turnate și produse finite cotează și au obținut beneficii economice semnificative.
3. Aplicarea nisipului ceramic în carcasa turbocompresorului
Temperatura de lucru la capătul turbinei carcasei turbocompresorului depășește în general 600 ° C, iar unele ajung chiar și la 950-1050 ° C.Materialul carcasei trebuie să fie rezistent la temperaturi ridicate și să aibă performanțe bune de turnare.Structura carcasei este mai compactă, grosimea peretelui este subțire și uniformă, iar cavitatea interioară este curată etc., este extrem de solicitantă.În prezent, carcasa turbocompresorului este în general realizată din oțel turnat rezistent la căldură (cum ar fi 1.4837 și 1.4849 din standardul german DIN EN 10295), și se utilizează și fontă ductilă rezistentă la căldură (cum ar fi standardul german GGG SiMo, americanul). fier nodular austenitic standard D5S, etc.).
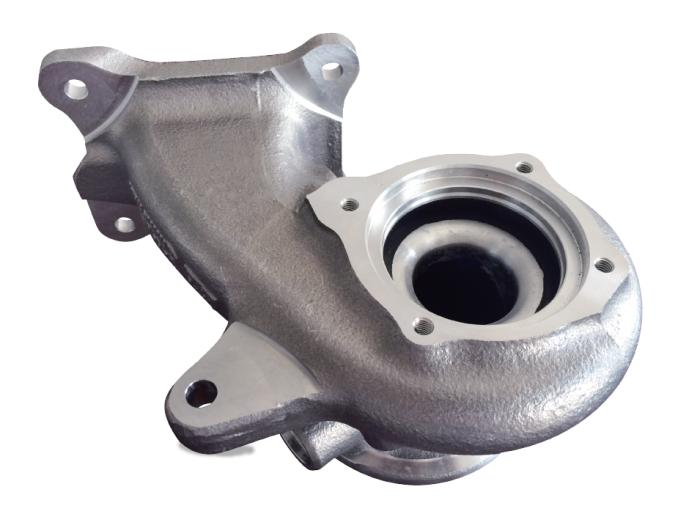
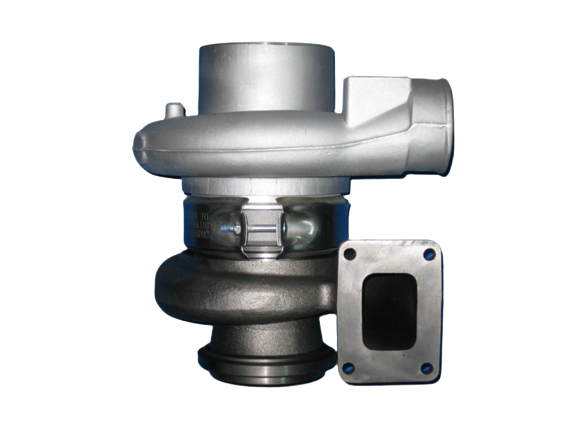
A carcasă turbocompresor motor 1.8 T, material: 1.4837, și anume GX40CrNiSi 25-12, compoziția chimică principală (%): C: 0.3-0.5, Si: 1-2.5, Cr: 24-27, Mo: Max 0.5, Ni: 11 -14, temperatura de turnare 1560 ℃.Aliajul are un punct de topire ridicat, o rată mare de contracție, o tendință puternică de fisurare la cald și dificultate mare de turnare.Structura metalografică a turnării are cerințe stricte privind carburile reziduale și incluziunile nemetalice și există și reglementări specifice privind defectele de turnare.Pentru a asigura calitatea și eficiența producției pieselor turnate, procesul de turnare adoptă turnarea miezului cu miezuri de coajă de nisip acoperite cu film (și unele miezuri de cutie rece și cutie fierbinți).Inițial, a fost folosit nisip de spălare AFS50, iar apoi a fost folosit nisip de siliciu prăjit, dar probleme precum lipirea nisipului, bavurile, fisurile termice și porii din cavitatea interioară au apărut în grade diferite.
Pe baza cercetărilor și testelor, fabrica a decis să folosească nisip ceramic.Achizitionat inițial finisat nisip acoperit (100% nisip ceramic), apoi achiziționat echipamente de regenerare și acoperire și optimizat continuu procesul în timpul procesului de producție, utilizați nisip ceramic și nisip de frecat pentru a amesteca nisipul brut.În prezent, nisipul acoperit este implementat aproximativ conform următorului tabel:
Proces de nisip acoperit cu nisip ceramic pentru carcasa turbocompresorului | ||||
Dimensiunea nisipului | Rata de nisip ceramic % | adaos de rășină % | Rezistența la încovoiere MPa | Debit de gaz ml/g |
AFS50 | 30-50 | 1,6-1,9 | 6,5-8 | ≤12 |
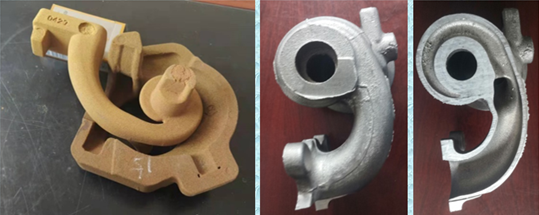
În ultimii câțiva ani, procesul de producție al acestei fabrici a funcționat stabil, calitatea pieselor turnate este bună, iar beneficiile economice și de mediu sunt remarcabile.Rezumatul este următorul:
A.Folosirea nisipului ceramic sau a unui amestec de nisip ceramic și nisip siliciu pentru a face miezuri, elimină defecte precum lipirea nisipului, sinterizarea, nervurile și fisurarea termică a pieselor turnate și realizează o producție stabilă și eficientă;
b.Turnarea miezului, eficiență ridicată a producției, raport scăzut nisip-fier (în general nu mai mult de 2:1), consum mai mic de nisip brut și costuri mai mici;
c.Turnarea miezului este favorabilă reciclării și regenerării generale a nisipului rezidual, iar recuperarea termică este adoptată uniform pentru regenerare.Performanța nisipului regenerat a atins nivelul de nisip nou pentru spălarea nisipului, ceea ce a realizat efectul de reducere a costului de achiziție al nisipului brut și de reducere a deversării deșeurilor solide;
d.Este necesar să se verifice frecvent conținutul de nisip ceramic în nisip regenerat pentru a determina cantitatea de nisip ceramic nou adăugat;
e.Nisipul ceramic are formă rotundă, fluiditate bună și specificitate mare.Când este amestecat cu nisip de siliciu, este ușor să provoace segregare.Dacă este necesar, procesul de aruncare a nisipului trebuie ajustat;
f.Când acoperiți filmul, încercați să utilizați rășină fenolică de înaltă calitate și folosiți diverși aditivi cu precauție.
4. Aplicarea nisipului ceramic în chiulasa motorului din aliaj de aluminiu
Pentru a îmbunătăți puterea automobilelor, a reduce consumul de combustibil, a reduce poluarea prin eșapament și a proteja mediul înconjurător, automobilele ușoare reprezintă tendința de dezvoltare a industriei auto.În prezent, piesele turnate pentru motoare de automobile (inclusiv motorul diesel), cum ar fi blocurile cilindrice și chiulasele, sunt în general turnate cu aliaje de aluminiu, iar procesul de turnare a blocurilor cilindrilor și a chiulaselor, atunci când se utilizează miezuri de nisip, turnare gravitațională a matriței de metal și presiune joasă. turnarea (LPDC) sunt cele mai reprezentative.
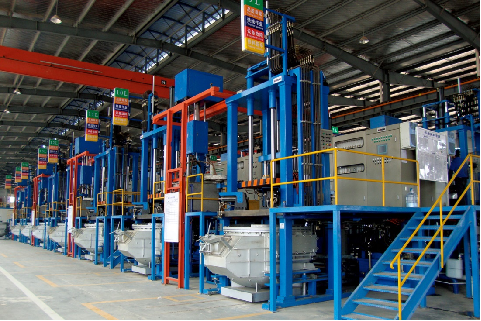
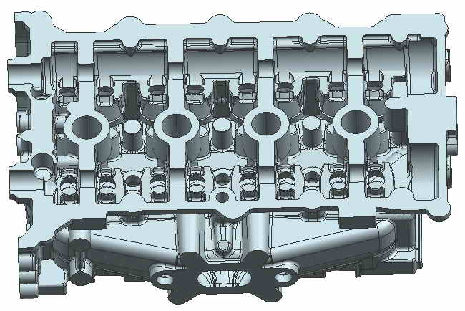
Miezul de nisip, nisipul acoperit și procesul de cutie rece a blocului cilindric din aliaj de aluminiu și turnării capului sunt mai frecvente, potrivite pentru caracteristicile de producție de înaltă precizie și la scară largă.Metoda de utilizare a nisipului ceramic este similară cu producția de chiulasă din fontă.Datorită temperaturii scăzute de turnare și a greutății specifice mici a aliajului de aluminiu, se folosește în general nisip de miez cu rezistență scăzută, cum ar fi un miez de nisip de cutie rece într-o fabrică, cantitatea de rășină adăugată este de 0,5-0,6%, iar rezistența la tracțiune este 0,8-1,2 MPa.Este necesar nisip de bază. Are o bună capacitate de pliere.Utilizarea nisipului ceramic reduce cantitatea de rășină adăugată și îmbunătățește foarte mult prăbușirea miezului de nisip.
În ultimii ani, pentru a îmbunătăți mediul de producție și a îmbunătăți calitatea pieselor turnate, există din ce în ce mai multe cercetări și aplicații ale lianților anorganici (inclusiv sticla de apă modificată, lianți de fosfat etc.).Imaginea de mai jos este locul de turnare al unei fabrici care utilizează nisip ceramic, liant anorganic, nisip, chiulasă din aliaj de aluminiu.
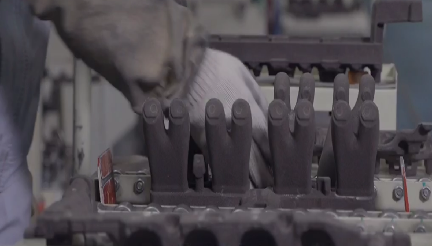
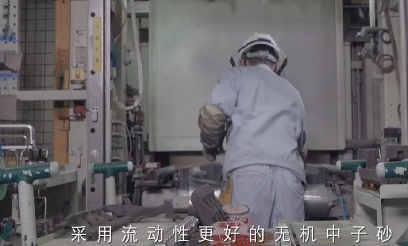
Fabrica folosește liant anorganic de nisip ceramic pentru a face miezul, iar cantitatea de liant adăugată este de 1,8 ~ 2,2%.Datorită fluidității bune a nisipului ceramic, miezul de nisip este dens, suprafața este completă și netedă și, în același timp, cantitatea de gaz generată este mică, îmbunătățește foarte mult randamentul piesei turnate, îmbunătățește colapsitatea nisipului de miez. , îmbunătățește mediul de producție și devine un model de producție ecologică.
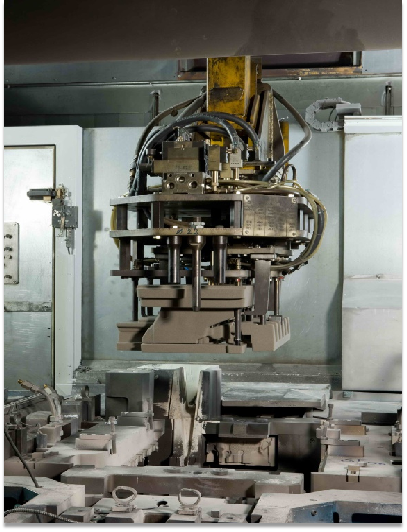
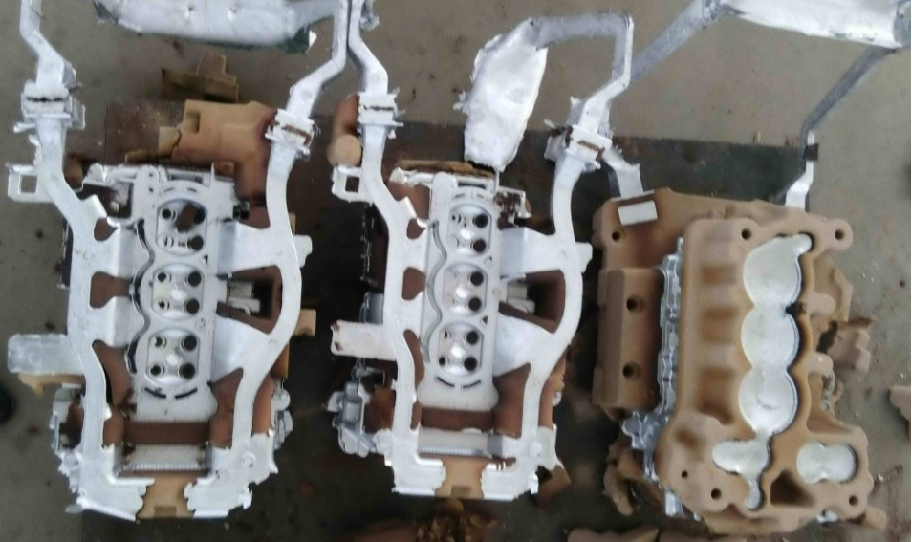
Aplicarea nisipului ceramic în industria de turnare a motoarelor a îmbunătățit eficiența producției, a îmbunătățit mediul de lucru, a rezolvat defectele de turnare și a obținut beneficii economice semnificative și beneficii bune pentru mediu.
Industria turnătoriei de motoare ar trebui să continue să crească regenerarea nisipului de miez, să îmbunătățească în continuare eficiența utilizării nisipului ceramic și să reducă emisiile de deșeuri solide.
Din perspectiva efectului de utilizare și a domeniului de utilizare, nisipul ceramic este în prezent nisipul special de turnare cu cea mai bună performanță cuprinzătoare și cel mai mare consum din industria de turnare a motoarelor.
Ora postării: 27-mar-2023